Qu’est-ce qu’une forge ?
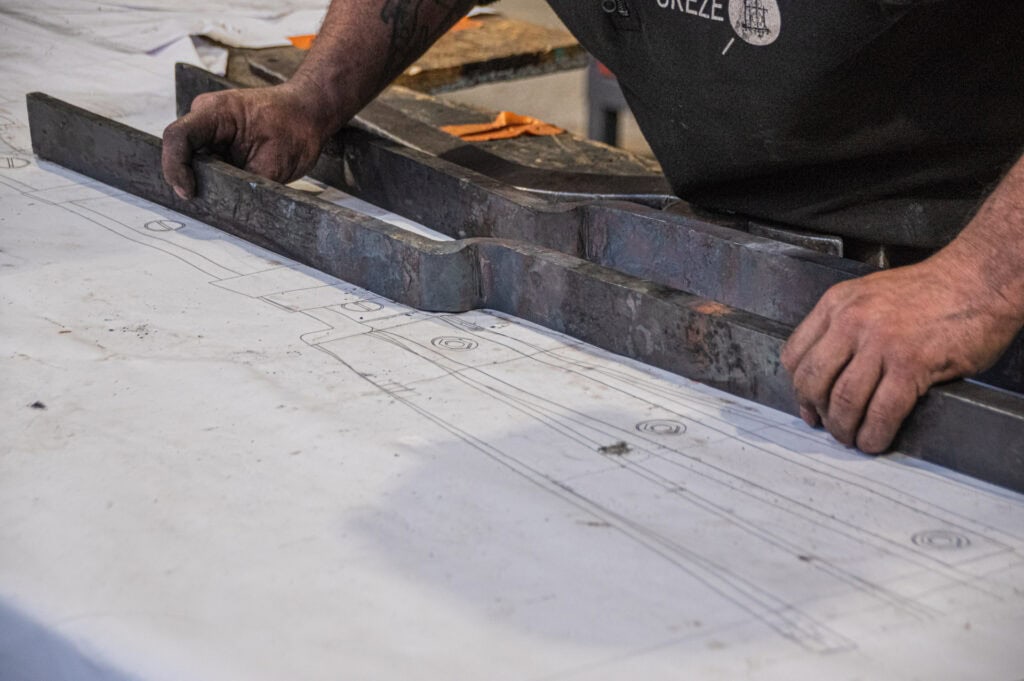
La forge : définition et fonctions
Une forge est un lieu où le métal est chauffé et façonné par des artisans ou des machines pour créer des objets en métal. Traditionnellement, une forge utilise un feu alimenté par du charbon, du bois ou d'autres combustibles pour chauffer le métal à des températures élevées, le rendant ainsi malléable pour être martelé, étiré ou plié selon les besoins.
Les différentes utilisations de la forge à travers les âges
La forge a joué un rôle crucial dans de nombreuses sociétés à travers les âges, offrant la possibilité de façonner le métal pour répondre à divers besoins et dans différents domaines.
Premièrement, La forge a été largement utilisée pour fabriquer une variété d'outils essentiels à la vie quotidienne, tels que des couteaux, des haches, des socs de charrue, des marteaux, des scies, des pinces et bien d'autres éléments qui a été ou bien est utilisé de nos jours.
Au cours de l’histoire, au sein de nombreuses civilisations, la forge était utilisée pour fabriquer des pièces métalliques utilisées dans la construction. Des pièces comme des clous, des charnières, des crochets, des gonds de porte, des barres d'armature et des ornements architecturaux.
Dans les sociétés agraires, la forge était utilisée pour fabriquer des outils agricoles, comme des charrues, des socs, des faucilles, des herses et des tondeuses à foin, qui étaient essentiels pour la culture des terres et la production alimentaire.
La forge a également été utilisée pour fabriquer des pièces pour les véhicules et les moyens de transport, tels que des pièces de chariots, des essieux, des clous de fer pour les chaussées, des roues et des pièces de locomotives.
Outre les éléments de la vie quotidienne, la forge a, au même titre, été à l’origine de nombreuses armes de guerre. En effet, cette utilisation date de l'Antiquité, des armes telles que des épées, des lances, des boucliers, des armures et des armes à feu. Ces armes étaient cruciales pour les armées et les guerriers à travers les époques.
Dans l’antithèse de ces créations précédentes, la forge a également été utilisée pour créer des objets artistiques et décoratifs, tels que des sculptures, des bijoux, des ustensiles de cuisine, des luminaires, des grilles et des portails décoratifs.
Ces exemples illustrent la diversité des utilisations de la forge à travers les âges et son importance dans le développement et la progression des civilisations humaines.
Composition d'une forge traditionnelle
Le foyer : cœur de la forge
Le foyer est souvent considéré comme le cœur de la forge, car c'est là que se déroule le processus de chauffage du métal et où se crée l'environnement nécessaire au forgeage. C'est là que le forgeron passe la majeure partie de son temps, travaillant le métal et créant des objets uniques à partir de simples morceaux de fer ou d'acier.
Le foyer est l'endroit où le combustible est brûlé pour produire de la chaleur. Cette chaleur est essentielle pour chauffer le métal à des températures élevées, le rendant ainsi malléable et facile à façonner. Dans le cœur de la forge, le forgeron peut contrôler la température du métal en ajustant la quantité de combustible brûlé dans le foyer. Cela lui permet de chauffer le métal à la température optimale pour le travail de forgeage.
Le foyer est généralement équipé d'un soufflet ou d'un système similaire pour fournir de l'air au feu. L'air alimente la combustion du combustible, augmentant ainsi l'intensité de la chaleur produite. Un bon contrôle de l'apport en air est essentiel pour maintenir la température du foyer à un niveau optimal.
Dans de nombreuses forges traditionnelles, le foyer sert également de surface de travail. Le métal chauffé peut être placé directement sur le foyer pour le martelage ou pour le maintenir à température entre les différentes étapes de forgeage. Le contrôle précis du foyer est essentiel pour garantir des résultats de forgeage de haute qualité.
Les soufflets : fournisseurs d'oxygène
Les soufflets sont des dispositifs utilisés dans une forge pour fournir de l'air au feu, ce qui alimente la combustion du combustible et augmente ainsi l'intensité de la chaleur produite. Bien qu'ils ne fournissent pas directement de l'oxygène, ils jouent un rôle crucial en fournissant de l'air nécessaire à la combustion. Cela est essentiel pour maintenir le feu en activité et chauffer le métal à des températures élevées pendant le processus de forgeage.
Les soufflets traditionnels se composent généralement d'une chambre en bois ou en métal avec une ouverture à une extrémité et une soupape de contrôle de l'air à l'autre extrémité. Lorsque le forgeron actionne le soufflet en appuyant ou en tirant sur la poignée, de l'air est aspiré dans la chambre par la soupape et expulsé à travers un tuyau vers le foyer de la forge. Ce mouvement d'air alimente la combustion du combustible et augmente ainsi la température du feu.
Les soufflets peuvent être actionnés manuellement par le forgeron ou par un assistant, ou ils peuvent être alimentés par des moyens mécaniques ou électriques dans les forges modernes. Quelle que soit la méthode d'actionnement, les soufflets jouent un rôle essentiel en fournissant l'air nécessaire pour maintenir le feu de la forge, ce qui en fait en effet des "fournisseurs d'air" plutôt que d'oxygène.
L'enclume et les marteaux : les outils fondamentaux
Dans une forge, l'enclume et les marteaux sont en effet considérés comme des outils fondamentaux.
L'enclume est une surface solide en métal sur laquelle le métal chauffé est placé et martelé pour le façonner. Elle est souvent fabriquée à partir d'acier ou de fonte, offrant une surface durable et résistante aux coups de marteau. L'enclume est généralement dotée de différentes formes et de diverses zones de travail, telles que des cornes arrondies, des pans plats et des entailles, permettant au forgeron de réaliser une variété de tâches de forgeage. L'enclume fournit également un support stable pour le métal pendant le processus de martelage, ce qui permet au forgeron de façonner avec précision le métal selon ses besoins.
Les marteaux sont les outils principaux utilisés par le forgeron pour frapper et façonner le métal chauffé sur l'enclume. Ils sont disponibles dans une variété de tailles, de formes et de poids, en fonction du type de travail à effectuer. Les marteaux utilisés en forgeage sont habituellement fabriqués en acier ou en métal résistant, avec des manches en bois, en fibre de verre ou en métal pour une prise en main confortable et sécurisée. Les marteaux sont utilisés pour étirer, plier, former et texturer le métal, ainsi que pour enfoncer des poinçons, des coins ou des matrices dans le matériau chauffé pour créer des formes complexes.
Ensemble, l'enclume et les marteaux constituent les outils de base dans une forge, permettant au forgeron de façonner le métal selon ses besoins pour créer une variété d'objets et de pièces métalliques. Ces outils sont essentiels pour le processus de forgeage et ont été utilisés depuis des siècles par les artisans métallurgistes à travers le monde.
Les pinces et tenailles : pour manipuler le métal chaud
Les pinces et les tenailles sont des outils indispensables dans une forge, utilisés pour manipuler le métal chaud en toute sécurité.
Les pinces sont des outils à mâchoires utilisés pour saisir et tenir fermement le métal chaud pendant le processus de forgeage. Elles sont généralement constituées de deux bras métalliques articulés à une extrémité et munis de mâchoires à l'autre extrémité. Les mâchoires peuvent avoir différentes formes et tailles en fonction de l'application, mais elles sont conçues pour offrir une prise ferme sur le métal sans le déformer. Les pinces sont utilisées pour manipuler le métal chaud entre le foyer de la forge et l'enclume, pour le tourner, le déplacer et le positionner selon les besoins du forgeron.
Les tenailles sont des outils similaires aux pinces, mais avec des mâchoires plus longues et souvent plus épaisses. Elles sont conçues pour manipuler des pièces métalliques plus grandes et plus lourdes, offrant une prise solide et sécurisée sur le métal chaud. Les tenailles sont souvent utilisées pour manipuler des pièces de métal plus volumineuses ou des morceaux de matériau chauffés à des températures extrêmement élevées. Elles offrent également une protection supplémentaire au forgeron en gardant ses mains à une distance plus sûre de la chaleur intense.
Ensemble, les pinces et les tenailles permettent au forgeron de travailler le métal chaud avec précision et sécurité, en évitant les brûlures et en assurant un contrôle total sur les pièces en cours de forgeage. Ces outils sont essentiels dans une forge pour garantir un processus de forgeage efficace et sécurisé.
Le processus de forgeage
Le chauffage du métal
Dans le processus de forgeage, le chauffage du métal est une étape fondamentale où le matériau est porté à une température élevée pour le rendre malléable et plus facile à façonner. Voici une explication plus détaillée de cette étape :
Avant de commencer le chauffage, le métal est généralement préparé en fonction de la pièce à forger. Il peut être scié, coupé ou préformé pour obtenir la forme désirée avant d'être chauffé. Le métal est placé dans le foyer de la forge, où le combustible est brûlé pour produire de la chaleur.
Le forgeron surveille attentivement la température du métal pendant le chauffage. La température à laquelle le métal est porté dépend du type de matériau utilisé et du processus de forgeage spécifique. Certains métaux nécessitent des températures plus élevées que d'autres pour devenir suffisamment malléables. Le métal est chauffé uniformément dans le foyer de la forge en le plaçant près de la source de chaleur. Il est souvent tourné ou déplacé régulièrement pour assurer une répartition uniforme de la chaleur sur toute sa surface.
Le forgeron peut utiliser différentes méthodes pour évaluer la température du métal, telles que l'observation de la couleur ou l'utilisation d'un thermomètre à infrarouge. Il est essentiel de chauffer le métal à la bonne température pour éviter qu'il ne devienne trop mou ou ne se fissure pendant le forgeage.
Une fois que le métal est chauffé à la température appropriée, il est retiré de la forge et placé sur l'enclume pour être martelé et façonné selon les besoins du projet de forgeage. Le chauffage du métal est donc une étape cruciale dans le processus de forgeage, car il prépare le matériau à être travaillé de manière efficace et précise.
Le façonnage par déformation plastique
Dans le processus de forgeage, le façonnage par déformation plastique est une technique utilisée pour modifier la forme du métal. En le comprimant ou en le martelant à chaud, ce qui le rend malléable et permet de lui donner la forme désirée.
Avant le façonnage par déformation plastique, le métal est chauffé à une température élevée dans une forge. Cette chaleur rend le métal plus mou et plus malléable, ce qui facilite sa manipulation et sa déformation.
Une fois que le métal est chauffé à la température appropriée, il est placé sur l'enclume de la forge, où il est comprimé sous l'action d'un marteau ou d'une presse hydraulique. La compression du métal le force à changer de forme, en le rapprochant de la forme finale désirée.
Le métal chaud peut également être façonné en le martelant à l'aide d'un marteau sur l'enclume. Le forgeron utilise des coups précis pour façonner le métal selon ses besoins, en l'étirant, en le pliant ou en le déformant pour obtenir la forme souhaitée. Pendant le façonnage par déformation plastique, le métal reste à une température élevée pour rester malléable. Cependant, il est important de contrôler le processus de refroidissement pour éviter la détérioration du métal ou la formation de défauts. Parfois, le métal est refroidi progressivement dans un bain d'huile ou d'eau pour maintenir sa structure et ses propriétés.
Une fois que le métal a été déformé plastiquement pour atteindre la forme désirée, il peut nécessiter une finition supplémentaire pour éliminer les imperfections et obtenir une surface lisse et uniforme. Cela peut impliquer le meulage, le polissage ou d'autres techniques de finition.
Le façonnage par déformation plastique est une technique essentielle dans le processus de forgeage, car elle permet de transformer le métal brut en pièces finies et fonctionnelles. Cette technique offre une grande flexibilité et permet de créer une variété de formes et de structures complexes à partir de simples barres ou plaques de métal.
Les techniques de forge : étirage, forgeage, pliage, perforation
L'étirage est une technique de forgeage qui consiste à allonger le métal en le tirant à travers une filière ou une matrice. Cette technique est généralement utilisée pour réduire la section transversale du métal et augmenter sa longueur. Pendant l'étirage, le métal est chauffé à une température élevée pour le rendre plus malléable, puis il est étiré à travers la filière à l'aide d'une presse ou d'un marteau. Cette technique est couramment utilisée pour fabriquer des barres, des fils et d'autres pièces allongées.
Le forgeage est la technique de base du processus de forgeage, qui consiste à frapper le métal chaud pour lui donner la forme désirée. Pendant le forgeage, le métal est chauffé à une température élevée pour le rendre malléable, puis il est martelé sur une enclume pour le façonner. Le forgeron utilise des marteaux et des enclumes pour frapper et déformer le métal selon les besoins du projet. Cette technique permet de créer une grande variété de formes et de structures, allant des pièces simples aux pièces complexes.
Le pliage est une technique de forgeage qui consiste à courber ou à tordre le métal pour lui donner une forme spécifique. Pendant le pliage, le métal est chauffé à une température élevée pour le rendre malléable, puis il est courbé, plié ou tordu selon les besoins. Cette technique est souvent utilisée pour créer des formes courbes ou des angles dans le métal, et elle est couramment utilisée dans la fabrication de pièces décoratives ou structurales.
La perforation est une technique de forgeage qui consiste à percer des trous dans le métal à l'aide d'un poinçon ou d'une matrice. Pendant la perforation, le métal est chauffé à une température élevée pour le rendre malléable, puis un poinçon est utilisé pour percer un trou à travers le matériau. Cette technique est couramment utilisée pour créer des trous de fixation, des ouvertures pour les passages de câbles ou des trous de ventilation dans les pièces métalliques.
Ces techniques de forgeage sont essentielles dans la fabrication de pièces métalliques, car elles permettent de transformer le métal brut en pièces finies et fonctionnelles. Chaque technique offre une flexibilité et une variété de formes, ce qui permet aux artisans métallurgistes de créer une large gamme de produits selon les besoins du projet.
Les matériaux et métaux forgés
Le fer et l'acier : les classiques
Le fer et l'acier sont largement utilisés dans le processus de forgeage en raison de leurs propriétés physiques et de leurs caractéristiques qui les rendent idéaux pour la fabrication de pièces métalliques.
Le fer et l'acier sont des matériaux relativement malléables, ce qui signifie qu'ils peuvent être facilement déformés et façonnés lorsqu'ils sont chauffés à des températures élevées. Cette malléabilité permet aux forgerons de créer une grande variété de formes et de structures complexes à partir de ces métaux.
Le fer et l'acier ont une bonne résistance à la chaleur, ce qui les rend adaptés au processus de chauffage nécessaire au forgeage. Ils peuvent être chauffés à des températures élevées sans se déformer ou perdre leurs propriétés mécaniques, ce qui permet aux forgerons de travailler le métal à des températures sur lesquelles il est malléable. Ces matériaux sont également très résistants, ce qui les rend adaptés à une utilisation dans des applications nécessitant une grande résistance mécanique. Les pièces forgées en fer et en acier peuvent supporter des charges élevées et des contraintes mécaniques importantes sans se déformer ou se briser, ce qui les rend idéales pour les applications dans lesquelles la durabilité et la robustesse sont importantes.
Ces propriétés en font des matériaux polyvalents pour la fabrication de pièces métalliques dans une variété d'applications industrielles et artisanales.
Les métaux non-ferreux et alliages spéciaux
Certains métaux non-ferreux, tels que l'aluminium, le cuivre, le bronze et le titane, ainsi que certains alliages spéciaux, sont naturellement résistants à la corrosion. Cela les rend idéaux pour les applications exposées à des environnements corrosifs, tels que les industries chimiques, maritimes ou aérospatiales.
Les métaux non-ferreux, comme l'aluminium et le titane, sont généralement plus légers que le fer et l'acier. Cette légèreté en fait des choix attrayants pour les applications sur lesquelles la réduction du poids est critique, comme dans l'aérospatiale, l'automobile et les équipements sportifs.
Certains métaux non-ferreux, comme le cuivre et l'aluminium, ont une excellente conductivité électrique et thermique. Cela les rend adaptés à une utilisation dans les applications électriques et électroniques, ainsi que dans les équipements de transfert de chaleur. Parmi les alliages spéciaux, certains sont développés pour répondre à des besoins spécifiques en matière de propriétés mécaniques, telles que la résistance à haute température, la résistance à la traction élevée, la ductilité ou la résistance à l'usure. Ces alliages sont utilisés dans des applications où les métaux traditionnels ne peuvent pas répondre aux exigences de performance.
Le bronze et le laiton, ainsi que certains alliages spéciaux, ont des propriétés esthétiques attrayantes, comme une belle couleur, une finition brillante ou des propriétés de patine naturelle. Ils sont souvent utilisés dans les applications architecturales et décoratives auxquellesl'apparence est importante. Les métaux non-ferreux offrent une gamme diversifiée de choix pour répondre aux besoins variés des applications industrielles et artisanales.
La forge artistique et la ferronnerie
La création d'œuvres d'art en métal
La création d'œuvres d'art en métal par le processus de forgeage est un processus complexe et créatif qui nécessite à la fois compétence technique et vision artistique.
Tout d'abord, l'artiste et l’artisan travaille en collaboration sur la conception de l'œuvre d'art, en élaborant des croquis, des modèles ou des dessins pour visualiser le résultat final. Cette étape implique également la planification des matériaux, des outils et des techniques de forgeage qui seront utilisés pour réaliser l'œuvre.
L'artiste sélectionne le matériau métallique approprié pour l'œuvre d'art en fonction de ses propriétés physiques, de ses caractéristiques esthétiques et de ses exigences fonctionnelles. Les métaux couramment utilisés pour la création d'œuvres d'art en métal comprennent l'acier, le cuivre, le bronze, l'aluminium et le laiton, ainsi que divers alliages spéciaux.
Avant de commencer le processus de forgeage, le métal est souvent préparé en fonction des besoins spécifiques de l'œuvre d'art. Cela peut inclure le découpage, le pliage, le chauffage et d'autres techniques de préparation pour obtenir la forme de base désirée.
L'artisan commence le processus de forgeage en chauffant le métal à une température élevée dans une forge. Une fois que le métal est chaud et malléable, il est martelé, étiré, plié et déformé sur une enclume pour lui donner la forme et la texture désirées. Cette étape peut impliquer l'utilisation de divers outils de forgeage, tels que des marteaux, des pinces, des ciseaux et des poinçons, ainsi que des techniques de martelage et de modelage spécifiques. Une fois que la forme de base de l'œuvre d'art est réalisée, l'artisan procède à la finition et aux détails finaux. Cela peut inclure le meulage, le polissage, le brossage, le ciselage, la soudure et d'autres techniques pour affiner les contours, ajouter des motifs, des textures et des finitions décoratives, ainsi que pour créer des joints et des assemblages solides. Une fois que l'œuvre d'art en métal est complétée, elle peut être finie avec un revêtement protecteur pour prévenir la corrosion ou pour obtenir une finition esthétique spécifique. Enfin, l'œuvre d'art peut être installée dans son emplacement final, que ce soit à l'intérieur ou à l'extérieur, comme une pièce autonome ou intégrée dans un environnement architectural ou paysager.
La création d'œuvres d'art en métal par le processus de forgeage est un processus complexe et gratifiant. Ce processus allie habileté technique, créativité artistique et vision esthétique pour produire des pièces uniques et durables qui inspirent et captivent les spectateurs.
Le rôle du forgeron dans l'artisanat moderne
Dans l'artisanat moderne, le rôle du forgeron reste essentiel malgré l'automatisation et l'industrialisation croissante de nombreux processus de fabrication.
Les forgerons sont souvent sollicités pour créer des pièces métalliques uniques et personnalisées, que ce soit pour des projets artistiques, architecturaux, décoratifs ou fonctionnels. Leur expertise leur permet de concevoir et de fabriquer des pièces sur mesure selon les spécifications et les préférences du client, ce qui garantit des résultats uniques et hautement personnalisés.
Les forgerons jouent un rôle important dans la préservation et la transmission des techniques traditionnelles de forgeage. Ils continuent à utiliser des méthodes artisanales ancestrales pour travailler le métal, perpétuant ainsi un savoir-faire artisanal précieux et contribuant à la préservation du patrimoine culturel. Bien que les techniques traditionnelles de forgeage soient toujours largement utilisées, de nombreux forgerons modernes intègrent également de nouvelles technologies et des méthodes innovantes dans leur pratique. Cela peut inclure l'utilisation de machines à commande numérique (CNC), de logiciels de modélisation 3D, d'imprimantes 3D et d'autres outils et technologies modernes pour concevoir, fabriquer et personnaliser des pièces métalliques de manière efficace et précise.
Le rôle du forgeron dans l'artisanat moderne est multifacette, combinant expertise traditionnelle, innovation technologique, collaboration interdisciplinaire et engagement envers la préservation et la transmission des savoirs artisanaux. Les forgerons continuent à jouer un rôle vital dans la création de pièces métalliques uniques, de haute qualité et hautement personnalisées, tout en contribuant à l'enrichissement de la culture artisanale contemporaine.
Conservation et sécurité en forge
Les impératifs de sécurité dans une forge
Travailler dans une forge présente divers risques inhérents aux hautes températures, aux outils tranchants et aux équipements lourds. Pour garantir la sécurité des forgerons et de tous les travailleurs, il est crucial de suivre des impératifs de sécurité stricte.
Les forgerons doivent porter des vêtements en coton épais ou en cuir pour se protéger contre les brûlures. Les matières synthétiques sont à éviter, car elles peuvent fondre et adhérer à la peau. Pour cela, des gants en cuir épais sont nécessaires pour manipuler les pièces chaudes et les outils. Les bottes à embout en acier protègent les pieds contre les chutes d’objets lourds et les éclats de métal. Enfin, les lunettes de protection sont indispensables pour éviter les projections de particules de métal ou de scories. Pour les travaux générant des fumées ou des poussières métalliques, un masque respiratoire adéquat est essentiel.
Les outils et équipements doivent être inspectés régulièrement pour détecter toute usure ou défaillance. Les marteaux, pinces et enclumes doivent être en bon état. Les machines, comme les forges électriques ou les marteaux-pilons, doivent faire l’objet d’une maintenance régulière selon les recommandations du fabricant.
L’espace de travail doit être aménagé de manière préventive à tout incident. Ainsi, une bonne ventilation est nécessaire pour évacuer les fumées et les gaz potentiellement dangereux. L’espace de travail doit être bien organisé pour éviter les encombrements et les risques de chute. Les chemins doivent être dégagés. Des zones spécifiques doivent être délimitées pour les activités dangereuses comme le forgeage, avec des panneaux de signalisation clairs.
Les travailleurs doivent recevoir une formation régulière sur les techniques de forgeage sécuritaire et sur l’utilisation des équipements. Des procédures d’urgence doivent être mises en place pour faire face aux incendies, brûlures et autres accidents. Tous les employés doivent être formés à ces procédures. Les nouveaux employés et les apprentis doivent être supervisés par des forgerons expérimentés jusqu'à ce qu'ils maîtrisent les techniques de sécurité.
Pour la prévention des incendies, des extincteurs appropriés doivent être facilement accessibles et les travailleurs doivent savoir comment les utiliser. Les matériaux inflammables doivent être stockés loin des sources de chaleur et des flammes ouvertes. Les flammes nues doivent être contrôlées en permanence et éteintes lorsqu’elles ne sont pas nécessaires.
Enfin, les déchets métalliques, les scories et les produits chimiques doivent être éliminés de manière sécurisée conformément aux réglementations locales. Les produits chimiques utilisés dans la forge doivent être correctement étiquetés et stockés dans des conteneurs sécurisés.
En suivant ces impératifs de sécurité, les forgerons peuvent minimiser les risques d'accidents et travailler dans un environnement plus sûr et plus sain. La sécurité doit toujours être une priorité dans toute activité de forgeage.
Entretien d'une forge et bonne gestion des équipements
Maintenir une forge en bon état de fonctionnement et gérer efficacement les équipements sont essentiels pour garantir la sécurité, la productivité et la longévité des outils et des installations
Avant chaque session de travail, effectuer une inspection visuelle des outils et des équipements pour repérer les signes d'usure, de fissures ou de déformations. Régulièrement, il est nécessaire de tester le fonctionnement des machines et des équipements motorisés pour s'assurer qu'ils opèrent correctement et sans bruit inhabituel.
Ensuite, les outils de coupe comme les marteaux, les ciseaux et les burins doivent être fréquemment affûtés pour garantir une performance optimale et sécurisée. Il est important de réparer ou remplacer immédiatement les outils endommagés ou usés pour éviter les accidents.
Les machines et les équipements mobiles doivent être régulièrement graissés et lubrifiés selon les spécifications du fabricant pour éviter l'usure prématurée. Après chaque utilisation, les machines sont nettoyées pour éliminer les résidus de métal, la poussière et les débris. Il y a une vérification régulière des systèmes de sécurité des machines, telles que les arrêts d'urgence et les dispositifs de verrouillage, pour s'assurer qu'ils fonctionnent correctement.
Au niveau organisationnel, il faut maintenir un espace de travail bien organisé où chaque outil a sa place. Cela réduit les risques de chutes et d'accidents. Une élimination régulière des déchets métalliques, des scories et autres débris est fondamentale pour maintenir un environnement de travail propre et sûr. Enfin, il faut stocker les matériaux de manière sécurisée, en utilisant des étagères et des bacs appropriés pour éviter les renversements et faciliter l'accès.
Les systèmes de ventilation et de filtration doivent être fréquemment nettoyés et les filtres remplacés pour garantir une évacuation efficace des fumées et des poussières. Il est nécessaire d’inspecter les conduits de ventilation pour s'assurer qu'ils ne sont pas obstrués et qu'ils fonctionnent correctement. Les surfaces de travail, comme les enclumes et les établis, doivent être nettoyées pour enlever les débris et les résidus métalliques.
Les forgerons et les employés doivent recevoir une formation continue sur l'entretien et la gestion des équipements. Connaître les meilleures pratiques et les procédures d'entretien est cruciale.
En suivant ces pratiques d'entretien et de gestion, une forge peut fonctionner de manière plus efficace et sécurisée, garantissant ainsi une production de haute qualité et la sécurité des travailleurs. La maintenance régulière et la gestion rigoureuse des équipements sont des éléments clés pour une forge prospère et durable.
Les forges aujourd'hui : challenges et innovations
L'impact de l'industrialisation sur la forge traditionnelle
L'industrialisation, marquée par le développement des technologies et des méthodes de production de masse, a eu un impact profond et multiforme sur la forge traditionnelle. Cet impact peut être analysé sous divers angles, tels que l'économie, la technique, la culture et l'environnement de travail.
L'industrialisation a introduit des méthodes de production de masse qui ont radicalement changé le paysage économique. Les forges traditionnelles, souvent petites et familiales, ne pouvaient pas rivaliser avec les grandes usines capables de produire des biens métalliques en quantités beaucoup plus importantes et à des coûts réduits. La production industrielle a réduit les coûts des produits métalliques, rendant les articles produits par les forges traditionnelles plus chers et moins compétitifs sur le marché.
L'introduction de machines comme les marteaux-pilons hydrauliques, les presses et les forges électriques ont automatisé de nombreuses tâches autrefois effectuées manuellement. Cela a permis une production plus rapide et plus efficace. L'industrialisation a favorisé le développement et l'utilisation de nouveaux matériaux et alliages, améliorant la qualité et la durabilité des produits métalliques.
L'industrialisation a profondément transformé la forge traditionnelle en introduisant des innovations techniques, en modifiant les structures économiques, et en impactant les aspects culturels et sociaux du métier. Bien que cela ait conduit au déclin de nombreuses forges traditionnelles, celles qui ont su s'adapter ont trouvé de nouvelles opportunités dans des marchés de niche où l'artisanat et la qualité sur mesure sont toujours appréciés.
La révolution numérique et les nouvelles techniques de forge
La révolution numérique a apporté des changements significatifs dans de nombreux secteurs, y compris celui de la forge. L'intégration de technologies numériques et de nouvelles techniques a transformé les pratiques traditionnelles, offrant des avantages en termes de précision, d'efficacité et de créativité.
Les logiciels de CAO (Conception assistée par ordinateur) permettent aux forgerons de créer des modèles 3D détaillés de leurs pièces avant même de commencer le processus de forgeage. Cela permet de visualiser et de peaufiner les designs avec une grande précision. Les outils de simulation permettent de prévoir le comportement des matériaux sous diverses conditions de forgeage, réduisant ainsi les erreurs et les essais physiques coûteux. Les machines-outils à commande numérique (CNC) peuvent être programmées pour réaliser des opérations de forgeage complexes avec une précision extrême, automatisant certaines étapes du processus traditionnel.
L'impression 3D permet de créer rapidement des prototypes de pièces forgées, facilitant les phases de conception et de test. Les imprimantes 3D peuvent également être utilisées pour fabriquer des moules précis et personnalisés pour le forgeage.
Une technique émergente consiste à déposer des couches de métal fondu pour former une pièce. Cette méthode combine des aspects de la forge traditionnelle avec des technologies de fabrication additive, permettant la création de formes complexes et de structures internes impossibles à obtenir par forgeage traditionnel.
Les capteurs intégrés et les dispositifs de l'Internet des objets (IoT) permettent une surveillance en temps réel des paramètres de forgeage, tels que la température, la pression et la déformation. Cela assure un contrôle précis et la possibilité d'ajuster les conditions en cours de processus.
Les algorithmes d'IA peuvent analyser de vastes quantités de données de production pour optimiser les paramètres de forgeage, améliorant ainsi la qualité et l'efficacité. Les systèmes basés sur l'IA peuvent détecter automatiquement les défauts dans les pièces forgées, augmentant la précision et réduisant le besoin d'inspections manuelles laborieuses.
La révolution numérique n'a pas remplacé la forge traditionnelle, mais l'a plutôt transformée et enrichie. Les forgerons contemporains peuvent désormais combiner des techniques ancestrales avec des outils numériques avancés, ouvrant de nouvelles possibilités créatives et industrielles.
La forge comme patrimoine culturel et technique
La forge est bien plus qu'un simple procédé de fabrication ; elle représente un riche patrimoine culturel et technique qui a traversé les âges et continue de jouer un rôle important dans la société contemporaine. Cet héritage se manifeste à travers l’histoire, l’artisanat, les traditions et les techniques qui se perpétuent et évoluent avec le temps.
La forge est un patrimoine culturel et technique inestimable, enraciné dans l'histoire, mais en constante évolution. Elle incarne un savoir-faire artisanal unique, transmis de génération en génération, et continue de s'adapter aux défis et aux opportunités du monde moderne. La préservation et la promotion de la forge sont essentielles pour maintenir ce lien vital avec notre passé tout en inspirant de nouvelles créations pour l’avenir.